Dzięki dotacji z NCBiR firma Amargo wraz z naukowcami opracuje nową technologię zbiorników kompozytowych, która rozwiąże realne potrzeby przemysłu
W konkursie „Ścieżka dla Mazowsza” organizowanym w ostatnich miesiącach przez Narodowe Centrum Badań i Rozwoju, który zakłada finansowanie prac badawczo-rozwojowych realizowanych na terenie woj. mazowieckiego, przedsiębiorcy mieli możliwość pozyskania łącznie 600 mln zł dotacji. Wśród nich znalazła się firma Amargo z Ożarowa Mazowieckiego, która wraz z naukowcami Wydziału Inżynierii Materiałowej Politechniki Warszawskiej oraz z Politechniki Wrocławskiej dzięki prawie 14 mln zł dotacji opracuje inteligentną konstrukcję ciśnieniowego zbiornika kompozytowego z uchylną dennicą.
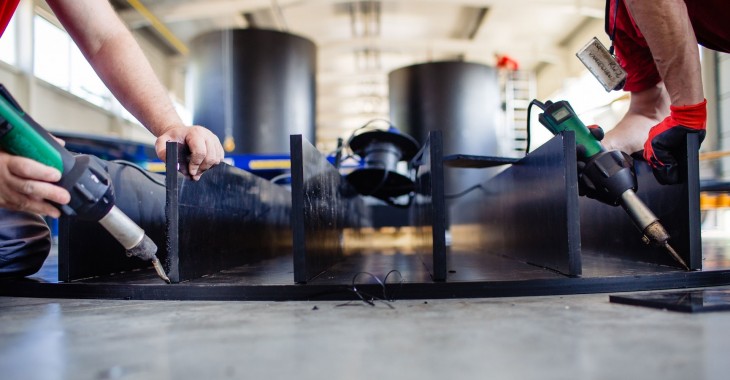
Procedura ubiegania się o dofinansowanie rozpoczęła się w sierpniu 2019 roku. W konkursie brały udział zarówno konsorcja przedsiębiorstw, jak i konsorcja przedsiębiorstw oraz jednostek naukowych, które miały na celu realizację badań przemysłowych, prac rozwojowych (obligatoryjnie) oraz prac przedwdrożeniowych.
Realizacja projektu badawczo-rozwojowego, który uzyskał 13 779 430,50 PLN dofinansowania z Narodowego Centrum Badań i Rozwoju rozpoczęła się 01.04.2020 r. i potrwa do 31.03.2023 r. Jego pełna wartość wyniesie 16 379 128,75 PLN. Oprócz firmy Amargo istotny wkład w realizację projektu będą mieli konsorcjanci – naukowcy z Wydziału Inżynierii Materiałowej Politechniki Warszawskiej oraz z Politechniki Wrocławskiej.
– Zasady konkursu były bardzo szczegółowe, ale bez wątpienia miało to swoje uzasadnienie. Sama procedura była przejrzysta i mimo znacznej ilości wymaganej dokumentacji opracowanie wniosku zajęło naszemu zespołowi projektowemu około 5 tygodni – to nie tak długo, biorąc pod uwagę złożoność projektu. Jego rozpatrzenie miało stosunkowo sprawny przebieg – decyzję o przyznaniu środków otrzymaliśmy nadzwyczaj szybko i bazując na poprzednich doświadczeniach związanych z uzyskiwaniem dofinansowań było to dla nas naprawdę miłe zaskoczenie – mówi Szczepan Gorbacz, prezes zarządu Amargo.
– Dzięki dofinansowaniu NCBiR będziemy mogli w znaczący sposób przyspieszyć realizację prac związanych z opracowaniem nowej technologii kompozytowych zbiorników z wysoce termo- i chemoodpornym linerem wykonanym z tworzyw z grupy fluorowców. Celem jest wytworzenie i zabudowanie niezwykle odpornej warstwy wewnętrznej, która to bezpośrednio będzie miała styczność z medium żrącym. Planujemy zabudowę materiałów takich jak poli(fluorek winylidenu) PVDF lub kopolimer etylen / chlorotrifluoroetylen E-CTFE. Do zespojenia obu materiałów przewidujemy zastosowanie warstwy sczepnej w postaci maty, siatki lub tkaniny włókien szklanych zatopionych w strukturze tworzywa. Nowa technologia pozwoli znacznie poszerzyć bieżącą ofertę produkcyjną, zapewniając praktycznie pełne pokrycie zapotrzebowania zakładów przemysłowych w zbiorniki magazynowe i procesowe oraz szeroką gamę specjalistycznych urządzeń i aparatów. Dotychczas, wykorzystując głównie tworzywa termoplastyczne typu polietylen oraz polipropylen, spotykaliśmy się z ograniczeniami w zakresie temperatur stosowania, ciśnienia oraz chemoodporności w pewnych zakresach wysoce agresywnych i utleniających związków chemicznych. Dysponując dodatkową technologią produkcji poprzez automatyczne ciągłe nawijanie programowanym oplotem włókna szklanego z jednoczesnym przesączaniem żywicą, zakres oferty Amargo staje się praktycznie nieograniczony – kontynuuje Szczepan Gorbacz.
– Nadmienię, iż równolegle realizujemy budowę nowej, wysokiej na 18 metrów hali produkcyjnej z czterema suwnicami. Oba projekty zapewnią Amargo zajęcie czołowej pozycji profesjonalnego producenta zbiorników chemoodpornych nie tylko w skali kraju, ale również Europy. Jako zespół TANK Think Tank jesteśmy bardzo dumni, że wspólnie z obiema Politechnikami możemy realizować tak ambitne zadanie – podkreśla.
Co wyróżnia nową technologię zbiorników kompozytowych
Celem projektu jest opracowanie inteligentnej konstrukcji ciśnieniowego zbiornika kompozytowego z dużą, uchylną dennicą. Jest to rozwiązanie, którego nie ma obecnie na rynku – istniejące ciśnieniowe zbiorniki kompozytowe wykonywane metodą nawijania włókna posiadają w dennicy jedynie niewielkie otwory. Z kolei te, które posiadają duży, otwierany właz, są konstrukcjami bezciśnieniowymi. Zarówno konstrukcję ciśnieniową i uchylną dennicę łączą w sobie jedynie zbiorniki wykonane ze stali nierdzewnej, kwasoodpornej lub powlekanej – konstrukcje te jednak cechuje bardzo wysoka masa i korozyjność materiału.
W ciśnieniowych zbiornikach kompozytowych wykonanie większego włazu jest utrudnione ze względu na konieczność zachowania ciągłości nawijanego włókna szklanego – tzw. rowingu. Miejsca, gdzie nie ma ciągłości włókna (miejsca przerwania włókna) – w przypadku pracy ciśnieniowej – obarczone są ryzykiem inicjacji pęknięć i uszkodzeń, a finalnie destrukcji oraz niebezpiecznych rozszczelnień.
Brak dużej, uchylnej dennicy wpływa na pewne ograniczenia w stosowaniu – m.in. utrudnia instalację grzałek, umieszczenie specjalistycznego materiału wypełnienia, np. węgla aktywnego celem realizacji zaplanowanych procesów technologicznych wewnątrz zbiornika / urządzenia, dostanie się do wnętrza zbiornika w celu inspekcji lub okresowego czyszczenia oraz realizacji innych czynności techniczno-procesowych wymagających znacznego dostępu i wolnej przestrzeni. Często jest to wymóg obligatoryjny lub zwyczajnie podyktowany racjonalnością codziennej eksploatacji i obsługi.
– Realizując nasz projekt badawczo-rozwojowy chcemy to zmienić – podkreśla profesor Anna Boczkowska z Politechniki Warszawskiej. – Opracowanie innowacyjnego sposobu realizacji technologii nawijania pozwoli nam na zamieszczenie w dennicy dużego włazu. Zadanie wiąże się z wieloma wyzwaniami, m.in. z zaprojektowaniem i wykonaniem specjalnego kołnierza i jego oplotu włóknem ciągłym, dobraniem odpowiedniego rozmieszczenia wiązek i przeplotów miedzy nimi tak, aby uzyskać optymalną pracę oplotu nośnego zbiornika. Włókna muszą być zaczepione za kołnierz łagodnie, bez ostrych krawędzi. Dodatkową trudność stanowi brak możliwości użycia części metalowych. Proponowana konstrukcja nie jest rozbieralna, a zatem musi posiadać oplot monolityczny. Kolejnym zagadnieniem technologicznym jest oczujnikowanie zbiornika w celu monitorowania stanów niebezpiecznych, takich jak: wyciek, rozszczelnienie, deformacja, pęknięcie, nadmierne lokalne uszkodzenia itp. – kończy profesor Boczkowska.
x
x
Podsumowując, nowa konstrukcja ciśnieniowego zbiornika kompozytowego będzie charakteryzowała się:
• wysoką odpornością chemiczną umożliwiającą pracę z trudnymi substancjami o dużym stężeniu, dającą pełne spektrum zastosowań bez ryzyka korozji i kosztownych renowacji,
• niską masą, która pozwoli na posadowienie na mniej wytrzymałym podłożu (brak dodatkowych kosztów związanych z wykonaniem płyty fundamentowej lub dodatkowego wzmocnienia podłoża czy podestu) oraz dzięki mniejszemu zużyciu paliwa ograniczy emisję CO2 i zminimalizuje cenę transportu (mniejsza masa umożliwi załadunek do pojazdów typu TIR),
• dużą, uchylną dennicą, która pozwoli na nieograniczony dostęp do wnętrza zbiornika.
Prace badawczo-rozwojowe – stan aktualny
Projekt składa się łącznie z 9 etapów. Pierwszym z nich są badania, w wyniku których określone zostaną warunki techniczne pracy i zabudowy zbiorników kompozytowych dla poszczególnych branż z sektora przemysłowego.
– Na pierwszym etapie prac, który rozpoczęliśmy z początkiem kwietnia br., niezwykle ważna jest dla nas opinia projektantów, technologów, konstruktorów i użytkowników instalacji przemysłowych, którzy pozwolą nam jeszcze lepiej poznać obszary, w jakich zbiorniki kompozytowe pomogłyby rozwiązać problemy, z którymi spotykają się w swojej codziennej pracy (m.in. z temperaturą, medium czy ciśnieniem). O części z nich już wiemy, natomiast zdajemy sobie sprawę, że ich spektrum jest bardzo szerokie. Pierwszym przykładem są aplikacje, w których zbiorniki projektowane jako monolit (ścianka tylko z tworzywa HDPE / PP-H) w warunkach wysokiej temperatury rzędu 60-80⁰C miałyby nieekonomicznie dużą grubość warstwy tworzywa. Czasami wręcz nie byłoby możliwe zgrzanie i pospawanie takich konstrukcji. Wówczas z pomocą przychodzą zbiorniki o ściankach multi-warstwowych – jest to tzw. konstrukcja hybrydowa: wewnątrz cienkie ultra odporne chemicznie i temperaturowo tworzywo pokryte jednostronnie zatopionym kaszerem + z zewnątrz wytrzymała konstrukcyjnie żywica z włóknem szklanym. Zależnie od charakteru pracy zbiornika zakładamy stosowanie wielu rodzajów żywic, począwszy od poliestrowych, poprzez vinyloestrowe – wskazuje Szczepan Gorbacz.
– Kolejnym przykładem są zbiorniki ciśnieniowe, nawet te uważane za magazynowe bezciśnieniowe, ale jak pokazuje praktyka – narażone na uderzenia hydrauliczne poduszki gazowej podczas rozładunków cystern metodą tzw. „przedmuchu”. Na temat wielu innych dodatkowych aplikacji stosowania zbiorników nowej generacji aktywnie prowadzimy rozmowy z uznanymi przedstawicielami rynku odbiorców oraz biur projektowych. Wszystkich, którzy swoim doświadczeniem chcieliby przyczynić się do rozwoju nowej technologii zapraszamy do udziału w przygotowanej ankiecie – kończy.
Zebrane na pierwszym etapie informacje pozwolą na wytypowanie systemów żywic i wzmocnienia do wykonania zewnętrznej warstwy zbiornika, a następnie przeprowadzenie badań ich właściwości mechanicznych, termicznych i termomechanicznych. Wyniki testów umożliwią przyjęcie założeń konstrukcyjnych do zbiornika eksperymentalnego, który będzie przedmiotem kolejnego etapu projektu. Poza badaniami wytrzymałościowymi zespół naukowy zrealizuje również badania przyspieszonego starzenia wytworzonych próbek w komorze starzeniowej, badania reologiczne oraz próby nawijania włókien na płaskie próbki wytypowanych tworzyw termoplastycznych, które wskażą na zdolności przetwórcze wybranych żywic. Na każdym etapie prac prowadzone będą również obserwacje mikroskopowe pozwalające na ocenę jakości wykonanych kompozytów.
Dokąd zmierza projekt, czyli co zyska przemysł
Branża przemysłowa już teraz widzi w nowej technologii ciśnieniowych zbiorników kompozytowych duży potencjał. Skorzystają z niej przede wszystkim sektory chemiczny, petrochemiczny, czy spożywczy, w których konieczne jest zapewnienie bezpiecznego magazynowania substancji żrących, agresywnych, niebezpiecznych i trujących o wysokiej reaktywności – takich jak np. związki silnie utleniające, kwas azotowy, fluorowodorowy, stężony kwas siarkowy 98%, mieszaniny zawierające związki chromu, chloru, w przypadku których zbiorniki z tworzyw termoplastycznych i bezciśnieniowe nie znajdują zastosowania. Dodatkowym miejscem zastosowania zbiorników nowej konstrukcji będą systemy i instalacje projektowane w tak zwanej technologii „Pure Plus” – systemy wysokiej i ultrawysokiej czystości.
Artykuł napisany na podstawie www.amargo.pl
Komentarze